INTRODUCTION
Globally rubber industry has been very active in its social commitments to control adverse effects of presence of such chemicals or physical effects that are dangerous to human body.
As a consequence of this several major rubber chemicals disappeared from the market though their own contribution to rubber processing and chemistry involved in making age resistant rubber products was way beyond doubts.
Major victims were Phenyl Alfa Naphthlylamine, Phenyl Beta Naphthylamine, DPPD, IPPD, Nitroso compounds, Isocynate type bonding agents, Morpholine derivatives in the class of sulphenamides and many others.
Focus of Bremels for their R&D programme was mainly based on:
a) Physical factors like vibrations, wet skidding etc.
b) Influence of micro-fine carbon black during mixing,
c) Health hazards like suspected carcinogenic and other harmful materials.
d) Selection of rubber chemicals in products that come in contact with food products.
(Non – marking solid cushioned tyres).
Main guiding directions come from organizations like EU associations and related authorities, FDA from USA and similar pollution control and health protection authorities also from India, Korea and Japan.
BREMELS R&D PROGRAMMES
Generally vibrations are developed by high speed movement. If contribution from tyres has to be considered, tyres with speed are generally more vulnerable to provide vibrations or contribute adversely the vibrations created by vehicle itself. Slow moving tryes like solid cushioned tyres or Press on band tyres are much less vulnerable to contribution to vibrations (These tyres are supposed to move at a very low speed and that too on well made indoor pavements). Fork-lift and industrial tyres have a maximum speed limit of 25 km/hour.
However, taking into account message found in EU Directive 2002/44/EC of the European Parliament and the Council of the European Union, Bremels undertook a programme to ensure that no slippage takes place when Bremels solid cushioned tyres are fitted on to the recommended rims.
CARBON BLACK PARTICLES
Micro fine particles of carbon black are yet another health hazard when carbon mixing is done on open mills. Bremels adopted two systems.
a) Use of carbon black master batches where carbon blacks are mixed in rubber at the latex stage and
b) Use of internal mixers like Banbury, Intermix or a Kneader; with chemical aid for dispersion.
CHEMICALS AND HUMAN HEALTH
Substantial quantities of OE – Extended Polybutadiene were used to get good abrasion resistance but this also developed low wet skid resistance. Experimentation led to drop Polybutadiene and still achieve required level of abrasion resistance by use of finer particle sized carbon blacks and special usage of precipitated silica. This was possible only because the maximum speed for solid cushioned and Press – on – Band tyres is limited to 25 km/hour.
Chemicals that were suspects for health hazards were replaced by chemicals that are safe. And finally, in the non – marking tyres only such chemicals were used in formulations that are cleared by FDA of USA for use in articles coming in long or continuous contact with food products.
VIBRATIONS AND HUMAN PERCEPTIONS
Dropping every synthetic rubber and opting only for NR (Natural Rubber) in the Solid Cushioned Tyres of Bremels is not by default but by design. Choice of NR to aid reduction in carrying over vibrations and shocks is fully supported by authentic technical literature. To quote just one reference we would like to highlight pages 28 and 29 of Hoffmann Rubber Technology Handbook that says –
“ The favourable elastic properties manifest themselves in very low damping (low hysteresis) and a low heat build-up in dynamic deformations. This behaviour combined with very short relaxation times, qualify NR especially for products which function in dynamic applications. These include vibration and suspension elements and tyres. The dynamic fatigue resistance of NR vulcanizates is also excellent”.
Bremels use only NR as the basic polymer in their compounding of components for solid cushioned tyres.
Fast moving objects create vibrations. Simplifying, an engine creates vibrations. Rubber components like “Vibra-mounts” are fixed into the vehicle systems to ensure that vibrations created by engine do not reach human bodies who act as passengers. Rubber based “Vibra-mounts” thus help damping. Typically the engine mountings or vibramounts are a sandwich of a rubber cured compound between two metal plates with solid bonding between metal and rubber.
Tyres whether pneumatic or solid have a component called cushion which is sandwiched between tread and core, both much harder compared to cushion.
Load – Deflection curves indicate quality norms of cushion. Lower the deflection better are vibration damping properties but lower is the load carrying capacity.
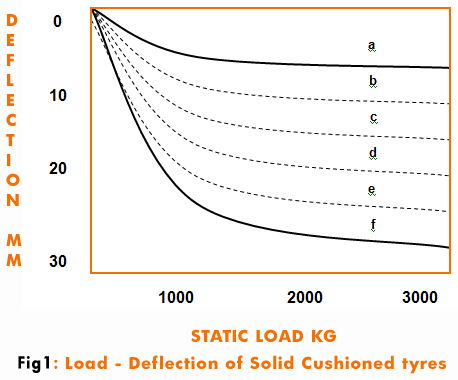
Bremels have fixed minimum and maximum levels of deflection that allows the tyre to meet ETRTO load specifications ‘a’ is the toughest tyre and ‘f’ is the softest tyre. b,c,d,e will depend on cushion (and obviously required damping effect)
a>b>c>d>e>f
for Load Bearing Capacity and
f>e>d>c>b>a for cushioning effect.
( > means “better than” )
An Interesting study of vibrations effect on humans is correctly exhibited by Reiher – Meister scale of human perception of vibrations (Fig. 2). Consider only solid cushioned tyres the best contribution from tyres will come when –
- Deflection (in load – deflection curves) is lowest and
- Tyres fit into rims without slip.
Bremels have mastered rubber technology that can provide any level of deflection within limits of loads specified by ETRTO and also ensure fitment of tyres into rims without slip.
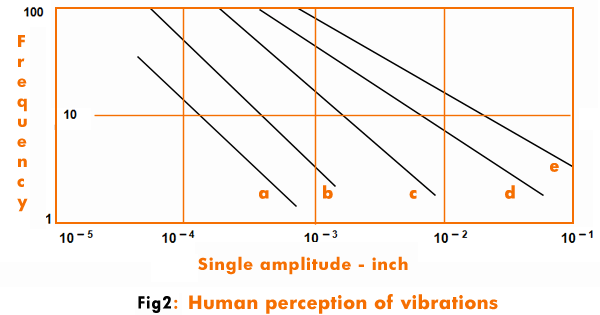
(Frequency is in cycles per second)
a – Imperceptible
b – Just perceptible
c – Easily Noticeable
d – Annoying
e – Unpleasant
Beyond e – Painful (Dangerous for short period)
As per EU Directive every work location has to select levels of damping to ensure that finally transferred vibrations are within specified limits. Bremels can help in selection of Load – Deflection curve for a given solid tyre size.
VIBRATION CONTROL
Contribution to vibration can be controlled or totally eliminated by ensuring that the grip of tyre bead zone into rim is perfectly satisfactory and shows no slip when the tyres are run with maximum specified loads at maximum permissible speed on a good concrete pavement.
This was achieved by creating compression in the bead zone, both vertically and laterally.
Lateral compression was achieved by providing higher bead zone width compared to same in the specified rim drawing.
Vertical compression was achieved by reducing the ID of tyre compared to rim ID.
Both settings can influence tyre width and tyre OD to a very small extent but this was taken care of by selecting these norms to fall in line with the requirement of ETRTO (European) specifications.
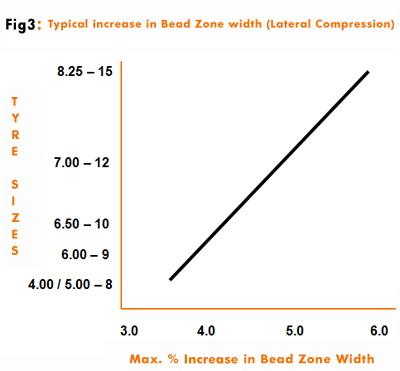
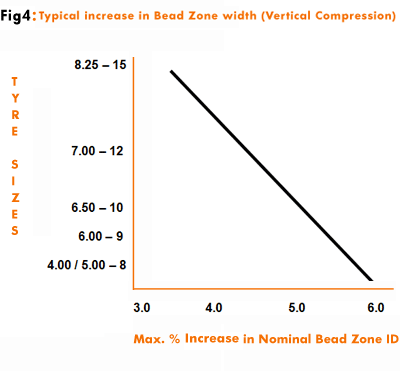
All the solid cushioned tyres produced with such compression showed zero slip. A strong chemical antifatigue agent used in the bead zone formulation ensured that development of fatigue was considerably reduced to avoid fatigue failures even after substantial ageing.
EU DIRECTIVE RELATED TO VIBRATIONS
Amongst several world standards one specific directive that covers this subject is Directive 2002 / 44 / Ec of the European Parliament and of the Council of the European Union (25 June 2002). This directive covers minimum health and safety requirements regarding the exposure of workers to the risks arising from physical agents (vibrations). Though this is directed to basically European community for safety, Hygiene and Health at work places, the requirements were studied and measures taken by Bremels certainly helped to reduce risks due to vibrations and shocks. Solid cushioned tyres produced by Bremels thus satisfy basic requirements of this directive.
This specifically satisfies the point 3 of the directive which says that it is necessary to introduce measures protecting workers from the risk arising from vibrations. Use of Bremels solid tyres can thus contribute to a great extent to minimize vibration effect.
It will not be out of place here to mention that several Indian companies are also signatories to worldwide authorities like Global Reporting Initiatives (GRI) which shows India’s awareness and commitment to Global requirements.
WET SKID RESISTANCE
(REFERENCE POINT 7, EU DIRECTIVE 2005 / 69 / EC)
Extensive work has been carried out by several tyre technologists on Wet-Skid resistance and while techniques are being developed to measure ‘skid’ and attempts made to correlate effects with likely causes, the subject of skid resistance has still remained highly complex. Rather than chasing, the quantitative regression equations to arrive at skid resistance mathematically it is more logical to consider observations and to arrive at guide information that may help tyre technologists in designing tyres to have best possible skid resistance. With this view in mind following observations have been considered in suggesting practical ways to handle skid.
- Wet slippery roads, contamination with debris such as general slush or mud, high speeds in cornering, defective braking system and above all bad old tyres are the frequent causes of skidding. Even the knowledge of this by a trucker in a country like India is as important as scientific aspects of this subject.
- High resilience is an important factor that contributes towards skid, (Particularly wet skid resistance which is poor with polybutadiene). A compound of polybutadiene having some 20% higher rebound compared to its blend with natural rubber will certainly have skid resistance as indicated by stopping distance lower by at least 10%. Addition of SBR or substitution by EPDM will therefore improve wet skid resistance. It is also possible to reduce rebound by means of compounding.
- Hardness contribution towards wet skid is also well acknowledged. Following data reveals this clearly.
Rubber |
Hardness |
Stopping distance (ft observed) |
BR |
62 |
180 |
NR / BR |
57 |
163 |
SBR / BR |
55 |
158 |
SBR |
52 |
151 |
- Loss of fine particles due to abrasion is also a contributing factor towards skid. Brittleness in a polymer therefore can be a serious cause of skidding tendency of a tyre. Stiffening of a polymer to a brittle state is associated with glass transition temperature and hence a polymer with TG closer to operating temperatures will be most dangerous as it will have a high potential of causing low temperature stiffness. With polymer having TG between 30 degree centigrade to 105 degree centigrade, wet skid resistance is known to inversely dependant on TG. With polymers that are available in India the order of merit can be established as under (sign > stands to indicate superior wet skid resistance) as far as wet skid resistance is concerned.

For tyres, therefore polymers are chosen from a range where TG is not higher than –40 degree centigrade. Even though temperatures like –40 degree centigrade are not experienced in India often, the low temperature stiffening component continues to be present to an extent in polymers even above their TG. This is really an important point. TG of required level can be obtained by blending those polymers in required ratio.
RESTRICTION (LEADING TO ELIMINATION) OF AROMATIC OILS
EU Directive 2005 / 69 / Ec has pointed out that materials like Aromatic oils used in oil extended rubbers and in compounding of rubber contain dangerous elements like Polycylic Aromatic Hydrocarbons presence of PAHS makes the extender aromatic oil suspects to be carcinogenic, mutagenic and toxic to reproduction.
The said Directive, though is restricted its application to only four selected sizes of Pneumatic tyres, Bremels undertook the required R&D work to replace the aromatic oil from basic polymers and in processing.
In USA, the OSHA (Occupational Safety and Health Administration) adopted the IARC (International Agency for Research on Cancer) report which classified untreated Naphtenic oils as carcinogenic and a user of such oils has to have a statement on the Material Safety Data Sheet (MSDS) that it contains untreated naphthenic oil which is considered carcinogenic. This is also applicable to oils which contain Polynuclear Aromatics (PNA).
ELIMINATION OF OIL EXTENDED RUBBER
Only common OE synthetic rubber used was SBR 1712 which contains 37.5 PHR of highly aromatic oil. Basic norms without its usage can be seen below. This was considered as a
basic change formula and other requirements were adjusted by selective use of fillers and other compounding materials. Basic comparison of SBR 1712 with our NR compound given below is good enough to understand the change. Actual component formulations cannot be disclosed for obvious reasons.
|
|
Natural Rubber |
|
A |
B |
Rubber |
137.50 |
100.00 |
100.00 |
Zinc oxide |
5.00 |
5.00 |
5.00 |
Stearic Acid |
2.00 |
2.00 |
2.00 |
Non Aromatic / Non Mineral
oil (Process oil 500) |
- |
15.00 |
15.00 |
Carbon Black (HAF) |
50.00 |
50.00 |
45.00 |
PPT Silica |
- |
Not disclosed |
Not disclosed |
Diethylene Glycol |
- |
1.00 |
1.00 |
CBS |
1.20 |
1.00 |
1.00 |
TMT |
0.20 |
0.15 |
0.15 |
Antioxidant |
1.00 |
1.00 |
1.00 |
Sulphur |
2.00 |
2.20 |
2.50 |
Properties
|
|
Natural Rubber |
|
A |
B |
ML 4 @ 100 deg. C |
45.0 |
48.0 |
45.0 |
Rheometric MI |
31.0 |
36.0 |
33.0 |
Rheometric ML |
22.0 |
26.0 |
23.0 |
Thermoplasticity |
9.0 |
10.0 |
10.0 |
Scorch – t2 (150 degree centigrade) |
2.5 |
2.4 |
2.4 |
Optimum cure t90 (150 degree centigrade) |
8.9 |
8.8 |
8.8 |
Cured at 150 deg. C for 30 minutes
|
|
Natural Rubber |
|
A |
B |
Tensile strength psi
Kg / cm2 |
3250 |
3300 |
3400 |
232.1 |
235.70 |
243.0 |
|
|
|
|
300% Modulus psi
Kg / cm2 |
1240 |
1260 |
1250 |
88.6 |
90.0 |
89.0 |
|
|
|
|
Elongation % Hardness Shore A |
550 |
580
|
570
|
54 |
57 |
55 |
|
Abrasion Index |
120 |
122 |
122 |
Basically the concerned EU directive is applicable to only a selected range of Pneumatic tyres probably due to reference to wet skid resistance. Nevertheless, even solid tyres use aromatic oils as processing aids and Bremels took quick steps to replace these oils with suitable ones (that do not have suspected polycyclic aromatic hydrocarbon).
PROCESS OILS IN COMPOUNDING
EU Directive 2005 / 69 / EC points out that not only the oil extended rubbers contain such extender oils that carry Polycyclic Aromatic Hydrocarbons that are not added intentionally but when such oils are used as a processing aid in rubber compounds they automatically find way to be present in the tyres and other products also.
Bremels undertook an exercise programme to totally replace Naphthanic and Aromatic oils
NON-MARKING TYRES
Rubber chemicals like accelerators, insoluble sulphur. Sulphur donors and antioxidants have to be within the limits cleared by FDA(section 121.2562 of the code of Federal Regulations) for rubber articles that come in repeated or continous contact with food products.
Bremels tread and sidewall compounds of non–marking solid cushioned tyres are designed to observe the required limits stipulated by FDA.
SUMMARIZING
- Bremels respects Global commitment to environmental safety and health hazards consideration as their social obligation.
- Bremels solid cushioned / POB tyres when mounted on prescribed rims will fit without slip thereby not contributing to vibrations.
- Bremels have chosen NR and suitable cushion compounds to minimize vibrations and improve damping.
- All known chemicals which are health hazardous including Aromatic oils are dropped from formulations with zero level targeted by December 2008.
- In Non – Marking tyres Bremels use only such chemical antioxidants, curing agents like Sulphur, accelerators and sulphur donors that are within usage limits cleared by FDA (USA) in rubber articles that come in long or continuous contact with food products.
- Bremels tread formulations are designed to offer best wet-skid resistance.
- Bremels R&D has many programmes in hand to serve to global needs.
While every effort has been made to see that data provided in this technical note is accurate; the company Bremels Rubber Industries Pvt. Ltd or the authors are in no way responsible for results of the application of this data as conditions of applications are beyond the control of the company or the authors.
|